Understanding the ways in which our actions have an environmental impact is a long journey, mostly a difficult and emotional one. I have been on my journey since 2008 when I undertook a Masters in Sustainable Design. Since then I have learnt a lot about what not to do, more recently I have found joy in what I can do in my everyday life to serve the environment. Honestly, in an area as complex, emotive and fast moving as environmental activism I have come to understand that the best way to make a positive impact is that which you are passionate about and which you have some control over.
Ceramics is as old as human civilisation, it is by definition 'fired earth'. As a modern-day discipline however, it is far removed from it's humble origins. My practice is embedded in industrial processes. I use plaster of paris moulds, finely processed liquid clay and glazes made from a multitude of industrially processed minerals, all fired in an electric kiln. I have a long way to go to reduce the impact that my pots make but I am striving to improve my processes as well as produce work that supports the ecosystem around me.
My work has been developed over several years and so making the changes to my making process is also taking me a long time. I have made a start though...
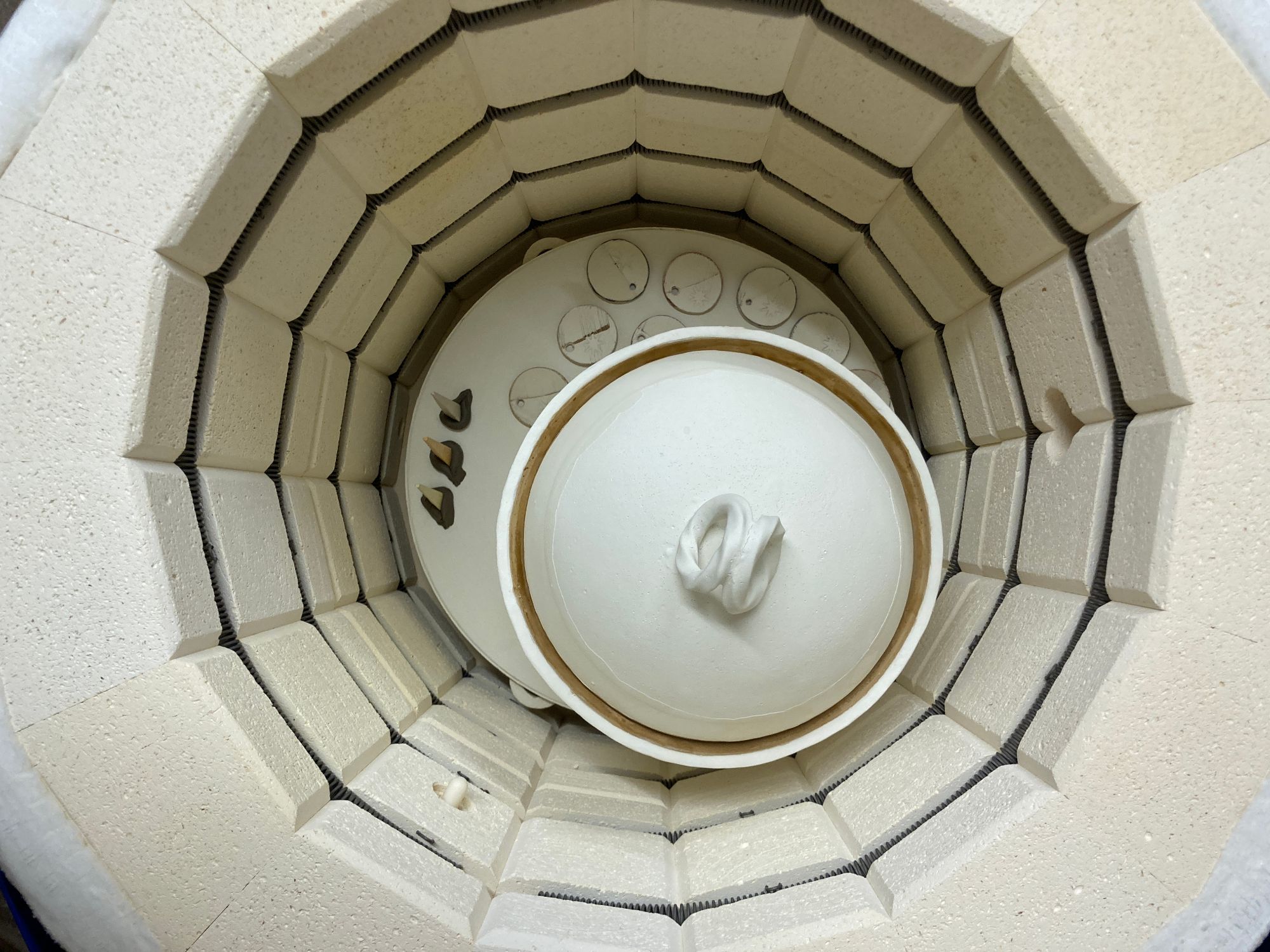
When buying my first ever kiln I chose a new design by British manufacturer Kiln Care. It runs on low ampage electricity, it is highly insulated to further reduce the power required to reach temperatures of 1240*c and beyond, and it will hopefully last me most if not all of my professional life. I hope to run it on solar power in the future.
Plaster of paris, or gypsom is an industrially mined natural material which is harmful when it degrades in the environment, there is no known non-hazardous disposal of this material so I am developing alternative production methods to avoid it altogether such as throwing on a wheel and utilising natural forms to press clay into rather than cast.
In my small studio I collect all of the waste sediment from glazing and I refire it to lock in volatile materials that would otherwise leach into the ground. I reclaim waste clay before it is fired to re-mix into slip and I repurpose unwanted pots in the garden. I have started to mix clay slip from powdered clay as a first step to producing my own clay from the natural Herefordshire red clay that exists all around me. Finally I hope to learn as much as I can about rock glazes so that I no longer have to use industrially produced and shipped minerals in my work.
There's a lot to be done, but bit by bit I'm getting there.